INFORMATION

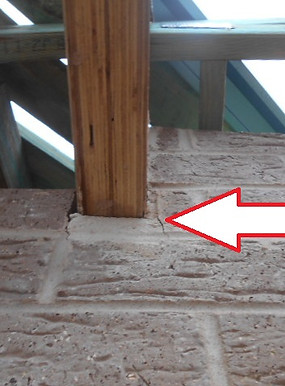
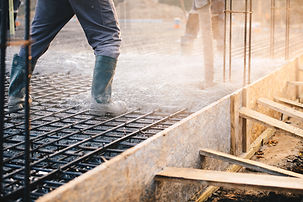
STAGE ONE FOOTINGS (SLAB)
​
Verify that the building's footings are built in accordance with the footing designed designs, the National Construction Code, and Australian Standard 2870.
A typical Footing Inspection has the inspector inspecting the footing preparation before concrete is poured. Footings are the lower structural elements of a building that lie directly on the foundation material and are virtually unreachable once poured. It's critical that footing preparations are done meticulously and in accordance with engineers' designs and specifications. Serious faults in footings can have disastrous consequences, which may not be discovered for years.
A Footing Inspection is strongly advised prior to pouring concrete for peace of mind. A typical Footing Inspection will reveal faults, defects, and non-compliance concerns, such as excavation, footing dimensions, steel reinforcement dimension and location, reinforcing supports, and clearances at service pipe footing penetrations. At lap and/or splice joints, all reinforcement should be fastened and knotted, if necessary.
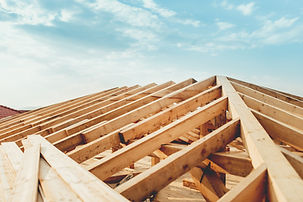
STAGE TWO WALLS AND ROOF FRAMES
​
An assessment to see if the wall and roof frames are structurally sound and meet the National Construction Code, Australian Standard 1684 for framing, engineering drawings, and framing plans.
A typical Frame Inspection entails the inspector inspecting the building's structural frame for quality of workmanship and compliance.
A Frame Inspection is required for peace of mind to ensure that the building frame structure is sound and meets design specifications.
Faults, defects, and difficulties connected to non-conformances will be revealed during an inspection. Inspections look for structural material compliance, stress grades, wind braces, lintel and lintel supports, point loads, horizontal wind beams, load transfer connections to the roof and/or floor diaphragm, tie-down, ceiling height, and secure and straight framing, among other things.
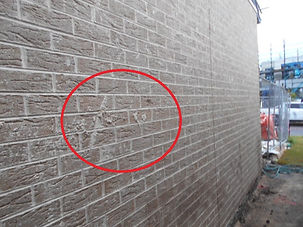
STAGE THREE - BRICKWORKS
​
What we look for in brickwork inspections:
-
Control the position of joints and waterproofing
-
Weep holes are holes in the ground that collect water
-
Control joints should be properly placed and sealed.
-
The strength and finish of the mortar
-
Bricks that have been chipped
-
First-floor perimeter flashing
-
Above the windows, there are weep holes.
-
Straight, plumb, and properly bearing on slab walls
-
Bed joints and perpends (intersecting walls)
-
Correct clearances for window sills
-
Piers that are half or full height
-
Brickwork snagging
-
Termite barrier is on the right track.
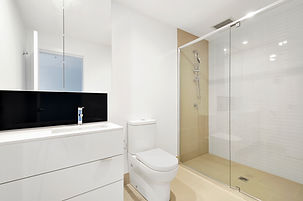
STAGE FOUR - WATERPROOFING AND INTERNAL LININGS
​
Waterproofing protects the sub-structure from leaks and rot by making bathrooms, balconies, and shower spaces resistant to water infiltration. This is usually accomplished with a paint-on membrane that provides a water-resistant coating. All wet areas must be waterproofed in accordance with the relevant Australian Standard, AS 3740 – Waterproofing of Domestic Wet Areas, and balconies must be waterproofed in accordance with AS 4654 – Waterproofing Membranes For External Above-Ground Use, according to the NCC/BCA (Building Code of Australia).
All internal fixtures, fittings and plaster boarding will be checked at this stage.
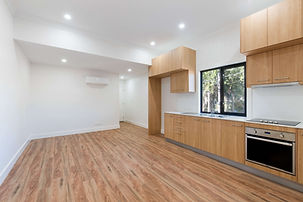
STAGE FIVE- HANDOVER
​
-
At this point of the inspection, we look at: All internal and external finishes and fittings throughout the home, plaster finish; carpentry and joinery items; door operation, and so on.
-
Bathroom fixtures are in good working order; taps are secure; plumbing is connected and operational; and the shower floor is flooded to test water tightness.
-
Check that kitchen items work properly, that taps are secure, that plumbing is connected and functional, that hot water is available (depending on utility status), and that bench tops are free of chips, cracks, and scratches, among other things.
-
Check for flaws in the floor coverings, such as carpet pulls, scratched wood or bamboo flooring, tiles, missed expansion joints, and poor craftsmanship.
-
Paint finish quality and completeness; inadequate coverage; chalky paint; poor plaster finish resulting in uneven surfaces, and so on.
-
Window glazing and frames are examined for scratches and defects, as well as for proper operation.
-
To ensure that no damage has occurred during the acid + pressure cleaning process, inspect the brickwork for cleanliness.